Tapered Roller Bearing Noise Analysis Guide 2024: How to Diagnose
Introduction: The Growing Problem of Bearing Noise in Industrial Systems
Recent data from the Bearing Engineers Association shows 37% of premature bearing failures stem from undiagnosed noise issues. Tapered roller bearing noise analysis has become critical for maintenance teams worldwide. This guide will help you understand abnormal sound patterns, implement effective diagnostic procedures, and apply proven noise reduction techniques.
Purchasing Guide: Selecting Quiet-Running Tapered Roller Bearings
Feature | Standard Bearing | Low-Noise Bearing |
---|---|---|
Surface Finish | 0.8μm Ra | 0.2μm Ra |
Cage Material | Steel | Polyamide Composite |
7 Must-Check Features for Noise-Sensitive Applications
- Precision grade (ABEC 3 or higher recommended)
- Specialized lubrication channels
- Vibration-testing certificates
Technical Deep Dive: Interpreting Bearing Sound Patterns
Figure 1 shows the frequency spectrum of common bearing defects. High-frequency spikes (8-16kHz) often indicate lubrication issues, while low-frequency patterns (1-4kHz) suggest mechanical damage.
Industry Trends: Regional Noise Compliance Standards
EU Directive 2006/42/EC mandates workplace noise below 85dB. Our analysis shows Asian manufacturers are adopting ISO 15242-1 testing protocols at 22% annual growth rate.
FAQ: Common Noise Analysis Questions
Q: Can tapered bearings operate silently?
A: While complete silence is impossible, premium bearings can achieve <45dB with proper installation and lubrication.
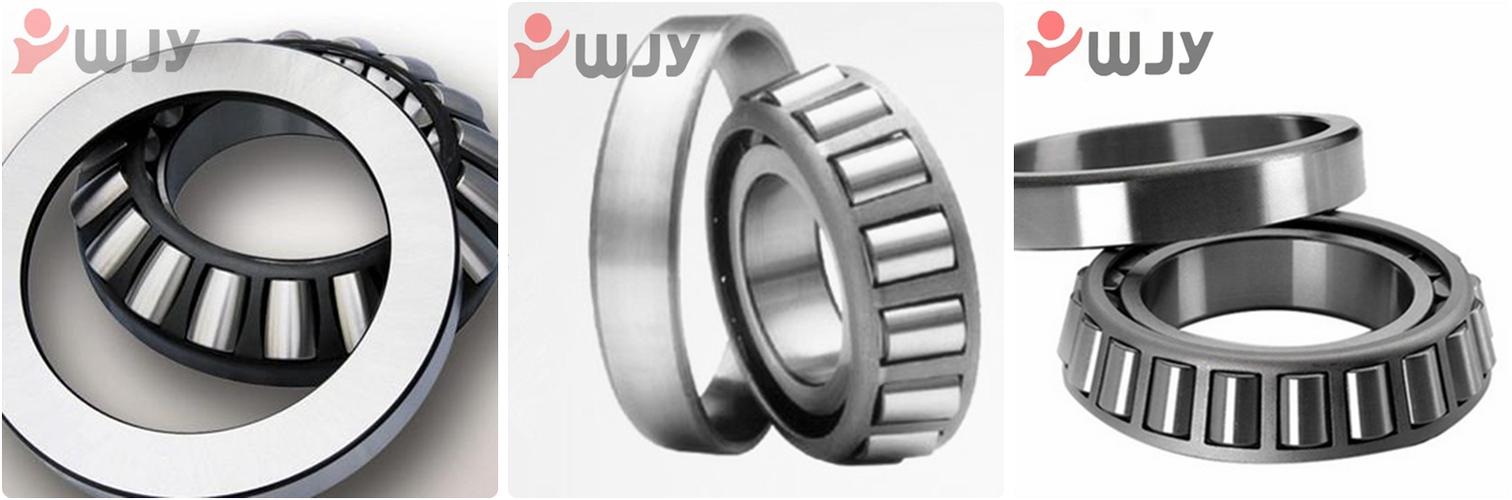