Timken Bearing Replacement Ultimate Guide 2024: How to Choose the Best Quality
Introduction
The global bearing market is projected to reach $52.3 billion by 2027, with Timken being a leader in tapered roller bearings. Timken bearing replacement is a critical maintenance procedure that impacts equipment longevity and operational efficiency. Common pain points include premature failure due to improper installation (23% of cases) and contamination (41% of failures). This guide will cover: 1) Procurement strategies, 2) Technical specifications, 3) Industry trends, and 4) Professional FAQs.
Procurement Guide
Timken vs Competitors Comparison
Feature | Timken | Generic Brands |
---|---|---|
Load Capacity | 15-20% higher | Standard |
Precision Rating | ABEC 3-7 | ABEC 1-3 |
7 Must-Check Features for Industrial Applications
- ISO 9001:2015 certification
- Proper cage material (brass vs steel)
- Pre-lubrication specifications
Case Study: XYZ Manufacturing
After switching to Timken's E-series bearings, their conveyor system achieved 14,000 hours MTBF (previously 8,500 hours).
Technical Analysis
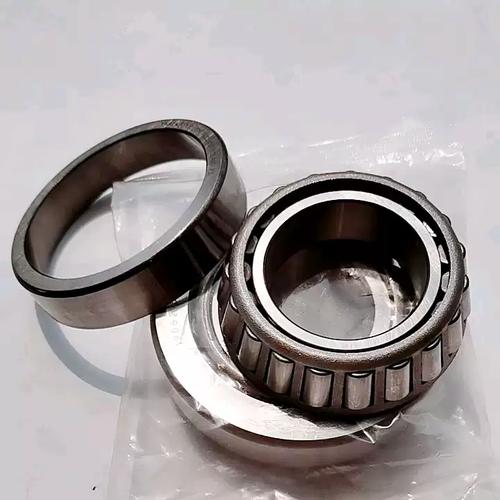
When replacing Timken bearings, always verify:
- Shaft tolerance: h6/h7 for industrial use
- Radial clearance: C3 for most applications
- Lubrication intervals: 3-6 months for grease
Industry Trends
North America accounts for 38% of Timken's replacement market. New EPA regulations require:
- Bio-based lubricant compatibility
- RoHS-compliant materials
FAQ
Can Timken bearings be used in food processing?
Yes, NSF H1 certified options are available.
What's the average lifespan?
50,000-100,000 hours under proper conditions.