Exploring the Essentials of Cylindrical Roller Bearings: Their Applications, Design Considerations, and Maintenance Practices
Introduction
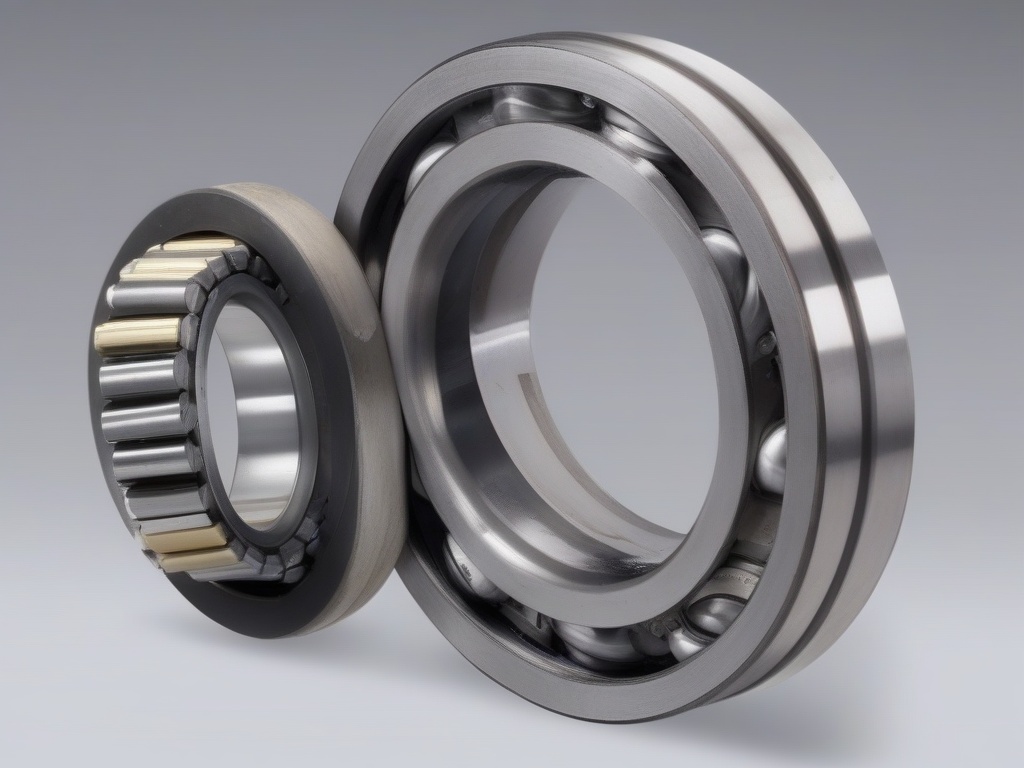
Cylindrical roller bearings, a crucial component in various industrial and mechanical systems, play a vital role in ensuring smooth and efficient operation. These bearings, which feature cylindrical rollers between inner and outer rings, are designed to handle radial loads and high-speed applications with precision and durability. In this article, we delve into the fundamentals of cylindrical roller bearings, exploring their applications, design considerations, and maintenance practices.
Applications of Cylindrical Roller Bearings
Cylindrical roller bearings are widely used in a range of industries, including automotive, aerospace, mining, and construction. Their versatility and ability to handle high loads at high speeds make them ideal for demanding applications such as transmissions, mills, and large-scale machinery. Here are some specific applications where cylindrical roller bearings excel:
1. Automotive Industry: In the automotive industry, cylindrical roller bearings are used in transmissions, differentials, and wheel hubs to ensure smooth and efficient power transmission. Their ability to handle radial loads and withstand high rotational speeds makes them essential for ensuring a smooth ride.
2. Aerospace Industry: In the aerospace industry, cylindrical roller bearings are critical components in various flight systems, including engines, transmissions, and landing gear. Their precision and reliability are paramount in ensuring the safety and performance of aircraft.
3. Mining and Construction: In mining and construction applications, cylindrical roller bearings are used in heavy-duty equipment such as cranes, excavators, and loaders. Their durability and load-carrying capacity enable these machines to operate efficiently in harsh environments.
Design Considerations for Cylindrical Roller Bearings
When selecting and designing cylindrical roller bearings, several factors must be taken into consideration to ensure optimal performance. Here are some key design considerations:
1. Load Capacity: The load capacity of the bearing is a critical factor that must be carefully determined based on the specific application. Overloading the bearing can lead to premature failure and reduce its lifespan.
2. Speed: Cylindrical roller bearings are designed to handle high-speed applications. However, excessive speeds can generate excessive heat and wear, affecting the bearing's performance. Therefore, it is important to select a bearing that can handle the desired speed range.
3. Precision: In applications that require high precision, such as in aerospace and machine tool industries, it is crucial to select a bearing with tight tolerances and high-quality materials. This ensures that the bearing can maintain its performance and accuracy over time.
4. Environment: The operating environment of the bearing should also be considered. Factors such as temperature, humidity, and contamination can affect the bearing's performance and durability. Selecting a bearing that is designed for the specific environment can help extend its lifespan.
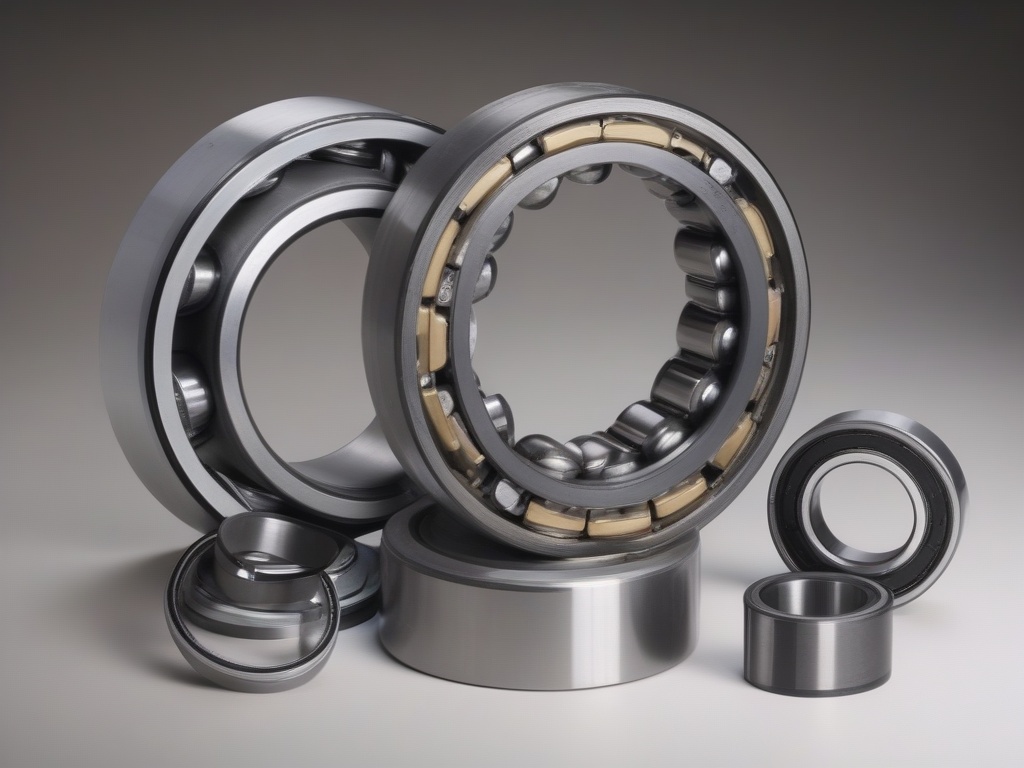
5. Material Selection: The material of the bearing components, including the rollers, inner and outer rings, and cage, should be selected based on the application's requirements. Materials such as steel, stainless steel, and ceramics are commonly used in cylindrical roller bearings due to their strength, durability, and resistance to wear.
Maintenance Practices for Cylindrical Roller Bearings
Proper maintenance is essential for ensuring the long-term performance and reliability of cylindrical roller bearings. Here are some best practices for maintaining these bearings:
1. Regular Inspection: Regularly inspect the bearing for signs of wear, cracks, or damage. Look for any abnormalities in the operation, such as excessive noise or vibration. Address any issues promptly to prevent further damage.
2. Lubrication: Ensure that the bearing is properly lubricated. Use the recommended lubricant type and quantity based on the manufacturer's specifications. Regularly check the lubricant level and replace it when necessary.
3. Cleanliness: Keep the bearing area clean and free of debris, dirt, or contamination. Contamination can lead to premature wear and failure of the bearing.
4. Proper Handling: Handle the bearing carefully during installation and removal to avoid damaging the components. Use the appropriate tools and techniques to ensure a secure and precise fit.
5. Storage: Store the bearing in a dry, clean, and temperature-controlled environment. Avoid exposure to moisture, dust, or chemicals that can damage the bearing materials.
Conclusion
Cylindrical roller bearings are essential components in various industrial and mechanical systems. Their ability to handle high loads and speeds with precision and durability makes them invaluable in applications such as automotive, aerospace, mining, and construction. By carefully considering design factors like load capacity, speed, precision, environment, and material selection, as well as implementing proper maintenance practices, you can ensure optimal performance and reliability of your cylindrical roller bearings.