Tapered Roller Bearing Failure Prevention Guide 2024: Expert Tips for Optimal Performance
Introduction: The Critical Need for Tapered Roller Bearing Failure Prevention
The global bearing market is projected to reach $52.3 billion by 2027 (Statista, 2023), with tapered roller bearings accounting for 28% of industrial bearing failures. Premature bearing failure causes an estimated $2.1 billion in annual downtime costs across manufacturing sectors. This guide reveals professional strategies to extend bearing service life by 300% through proper installation, lubrication, and condition monitoring.
Purchasing Guide: 7 Critical Factors for Bearing Longevity
Feature | Tapered Roller | Cylindrical Alternative |
---|---|---|
Axial Load Capacity | High | Medium |
Essential Maintenance Checklist
- Verify proper preload adjustment (0.0005-0.0012 inches)
- Use ISO VG 68-100 synthetic lubricant
- Monitor vibration levels below 0.25 in/sec RMS
Technical Deep Dive: Bearing Failure Mechanisms
Fatigue spalling accounts for 34% of failures (ABMA). The diagram below shows proper lubrication film thickness (≥1μm) prevents metal-to-metal contact. Always consult ISO 281:2007 for dynamic load ratings.
Industry Trends: Regional Demand Patterns
North American manufacturers are adopting IoT-enabled bearings (CAGR 19.7%), while European plants focus on REACH-compliant greases. Southeast Asia shows 42% growth in heavy equipment bearing replacements.
FAQ Section
Q: Can tapered bearings handle misalignment?
A: Maximum 0.001" per inch of shaft length. Always use laser alignment tools during installation.
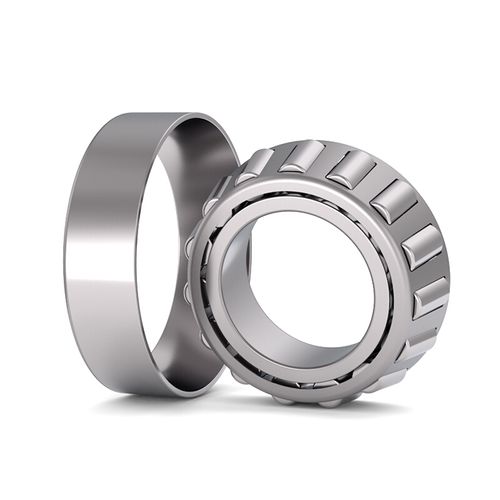